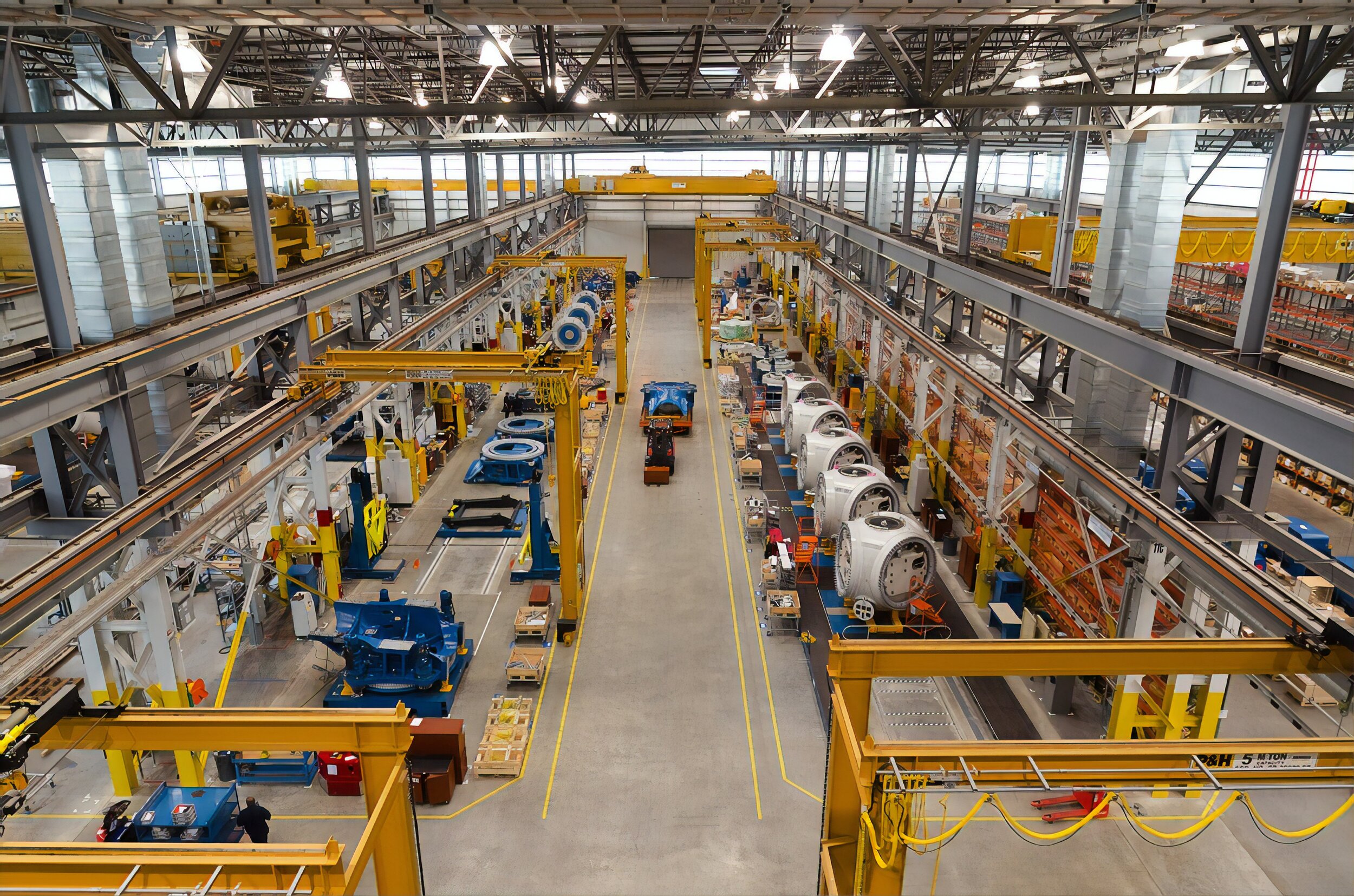
Case study: Manufacturing - Sydney
Background
An international textile manufacturer looking to digitalise processes in their Sydney plant, due to growing complexity in production.
Reasons for implementation
Using large weaving machines, with up to 600 spools of thread at a time, they produce an ever-increasing number of textile patterns. The team had developed a complex system using stickers, with combinations of colours, letters, and numbers; to help determine which exact colour thread was to be loaded in each position. The process was prone to errors, as staff loading the bobbins would need to constantly cross-reference the sticker codes, against a pattern chart.
Solution
FutureShelf was approached to help them improve efficiency and reduce errors. Using our digital price label technology, a bespoke solution was developed for their unique and specific needs. This was then tested on a proof of concept pilot, before being rolled out to the rest of production.
The solution involved an Electronic Shelf Label (ESL) fixed to each bobbin position, via an adhesive stand (one of our standard label accessories). An excel spreadsheet pattern file was then loaded into Shopweb (our Pricing Software Platform), which then automatically pushed the correct pattern information to each electronic label screen.
The information included a unique position ID, pattern name and correct thread. Once the ESL had successfully updated, the team could immediately load the correct threads, without needing to refer to and cross-reference the pattern chart.
Outcomes
The pilot proved a great success, with significantly lower error rates and increased working efficiencies.
For stage 2, FutureShelf was engaged to enhance their pattern spreadsheets, to enable the direct sending of patterns to the Shopweb API, with a single click. This optimised process is currently being rolled out to the rest of the manufacturing machines and will be driving even greater accuracy and efficiency.